Кисү процессында, кисүче көч аркасында, нечкә стенаны деформацияләү җиңел, нәтиҗәдә эллипс яки "бил" күренеше кечкенә урта һәм зур очлары белән.Моннан тыш, нечкә диварлы кабыкларны эшкәртү вакытында җылылыкның начар таралуы аркасында җылылык деформациясен җитештерү җиңел, бу өлешләрнең эшкәртү сыйфатын тәэмин итү авыр.Түбәндәге өлешләрне кысу гына түгел, эшкәртү дә авыр.Шуңа күрә махсус нечкә диварлы җиң һәм саклагыч вал эшләнергә тиеш.

Pанализ
Рәсемдә күрсәтелгән техник таләпләр буенча, эш өлеше корыч торба белән эшкәртелә, эчке тишекнең һәм тышкы стенаның өслеге тупаслыгы Ra1,6 μ м.Аны борып тормышка ашырырга мөмкин, ләкин эчке тишекнең цилиндриклыгы 0,03 мм, бу нечкә диварлы өлешләргә югары таләпләр таләп итә.Масса-күләм җитештерүдә процесс маршруты түбәндәгечә тупас: буш - җылылык белән эшкәртү - бетү йөзен әйләндерү - әйләнәне әйләндерү - эчке тишекне әйләндерү - сыйфат тикшерүе.
"Эчке тишек эшкәртү" процессы сыйфат белән идарә итүнең ачкычы.Кабыкның эчке тишеген цилиндрик нечкә диварсыз кискәндә 0,03 мм цилиндр тәэмин итү кыен.
Тишекләрне әйләндерү өчен төп технологияләр
Тишекләрне әйләндерүнең төп технологиясе - катгыйлык һәм эчке тишек әйләндерү коралларын чип чыгару проблемаларын чишү.Эчке тишек әйләндерү коралының катгыйлыгын яхшырту өчен түбәндәге чаралар күрелергә тиеш:
1) Корал тоткычының кисемтәләр мәйданын мөмкин кадәр арттыру.Гадәттә, эчке тишекне әйләндерү коралының очлары корал тоткычы өстендә урнашкан, шуңа күрә корал тоткасының секция мәйданы тишекнең секция мәйданының 1/4 өлешеннән кимрәк, түбәндәге рәсемдә күрсәтелгәнчә.Эчке тишекне әйләндерү коралының очлары корал тоткасының үзәк сызыгында урнашкан булса, тишектәге корал тоткасының бүлекчәсе түбәндәге рәсемдә күрсәтелгәнчә зурайырга мөмкин.

2) Корал тоткасының озын озынлыгы эш кисәгенең озынлыгыннан 5-8 мм озын булырга тиеш, корал тоткасының катгыйлыгын арттыру һәм кисү вакытында тибрәнүне киметү.
Чипны чыгару проблемасын чишегез
Ул, нигездә, кисү агымының юнәлешен контрольдә тота.Каты борылыш кораллары чипның эшкәртелүен өскә агызуны таләп итә (алгы чип).Шуңа күрә, түбәндәге рәсемдә күрсәтелгәнчә, уңай тишек белән эчке тишек әйләндерү коралын кулланыгыз.
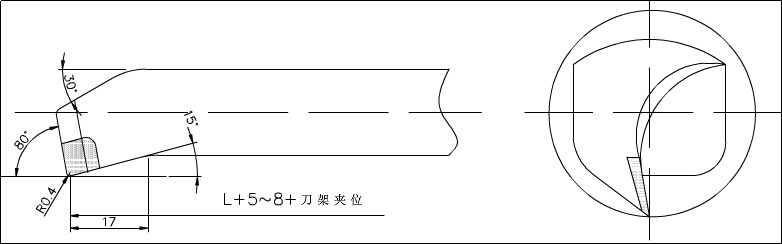
Яхшы борылыш процессында алгы чипны үзәккә юнәлтү өчен чип агымы юнәлеше кирәк (тишек үзәгендә чип чыгару).Шуңа күрә, коралны кискенләштергәндә кисү кырының тарту юнәлешенә игътибар бирелергә тиеш.Чипны чыгару ысулы алга омтылган дугага иярергә тиеш.Түбәндәге рәсемдә күрсәтелгәнчә, хәзерге M тибындагы нечкә әйләндерү коралы эретү YA6 яхшы бөкләнү көченә, киемнең каршылыгына, тәэсирнең катгыйлыгына, корыч белән ябышуына һәм температурага чыдамлыгына ия.

Тегермән вакытында эшкәртү дугасы буенча (коралның аскы сызыгы аркасы буенча), алгы почмак 10-15 ° дугага, ә арткы почмагы дивардан 0,5-0,8 мм.C кисүче кыр почмагы k юнәлешендә § 0,5-1, В ноктасында чип кыры буенча R1-1.5.Икенчел арткы почмак 7-8 ° ка тарту өчен яраклы.Чүп-чарны тышка чыгару өчен, E ноктасының эчке читендәге AA ноктасын түгәрәккә тарт.
Pэшкәртү ысулы
1) Вал калканнары эшкәртү алдыннан ясалырга тиеш.Вал саклаучының төп функциясе - нечкә диварлы җиңнең борылган эчке тишеген оригиналь размер белән каплау һәм аны алгы һәм арткы үзәкләр белән төзәтү, ул тышкы түгәрәкне деформациясез эшкәртә ала һәм эшкәртү сыйфатын саклый. һәм тышкы түгәрәкнең төгәллеге.Шуңа күрә, валны саклауны эшкәртү нечкә диварлы корпус эшкәртүнең төп бәйләнеше булып тора.
45 #валны саклап калу өчен углерод структур түгәрәк корыч;Ахыр йөзне әйләндерегез, В формасындагы үзәк тишекләрне ике очында ачыгыз, тышкы түгәрәкне тупас итегез һәм 1 мм рөхсәт калдырыгыз.Heatылылык белән эшкәртү, сүндерү һәм температура, үзгәртеп кору һәм яхшы борылыштан соң, тарту өчен 0,2 мм пособие сакланырга тиеш.Ushedимерелгән ялкын өслеге HRC50 катылыгы белән кабат җылылык эшкәртелергә тиеш, аннары цилиндрик тарткыч белән җиргә төшерелә, түбәндәге рәсемдә күрсәтелгәнчә.Төгәллек канәгатьләнерлек булырга тиеш һәм беткәч җиңел булачак.

2) Эш кисәген эшкәртүне берьюлы тәмамлау өчен, тупас яралгы кысу урыны һәм кисү рөхсәте булырга тиеш.
3) Беренчедән, җылылык белән эшкәртү, температура һәм формалашканнан соң, йон яралгының катылыгы HRC28-30 (эшкәртү диапазонында).
4) Борылыш коралы C620.Беренчедән, алгы үзәкне шакмак конусына урнаштырыгыз.Нечкә диварлы җиңне кысканда эш кисәгенең деформациясен булдырмас өчен, түбәндәге рәсемдә күрсәтелгәнчә, ачык калын калын җиң өстәлә.

Масса-күләм производствоны саклап калу өчен, нечкә диварлы кабыкның тышкы боҗрасының бер очын бертөрле размерга эшкәртәләр, линейка күчәр белән кысыла, һәм сыйфатын яхшырту өчен эчке тишекне әйләндергәндә нечкә диварлы кабык кысыла. һәм зурлыгын саклау.Кисүче җылылыкны исәпкә алып, эш кисәгенең киңәю күләмен үзләштерү кыен.Эш кисәгенең җылылык деформациясен киметү өчен җитәрлек кисүче сыеклык кертелә.
5) Эш кисәген автоматлаштырылган өч иҗек чәк белән кысып, соңгы битне әйләндерегез, тупас машина эчке түгәрәк.Ахыр әйләнеше - 0,1-0,2 мм.Саклаучы валның комачаулык таләпләренә туры китереп кисү өчен пособие эшкәртү өчен финиш борылыш коралын алыштырыгыз.Эчке тишекне әйләндерү коралын алыгыз, сакчы валын алгы үзәккә кертегез, озынлык таләпләре буенча койрык үзәге белән кысыгыз, цилиндрик борылыш коралын әйләндереп алыгыз, аннары рәсем таләпләренә туры китереп борылыгыз.Тикшерү үткәннән соң, киселгән пычакны кирәкле озынлыкка карап кисегез.Эш кисәге өзелгәндә кисүне шома итәр өчен, кисү кыры иелергә һәм эш кисәгенең соңгы йөзен шома итәр өчен җиргә салырга тиеш;Сакчы валының кечкенә өлеше бушлыкны киметү һәм кечерәк тарту өчен кулланыла.Саклагыч вал эш кисәгенең деформациясен киметү, тибрәнүдән саклап калу, егылу һәм бәрелү сәбәпләрен кисәр өчен кулланыла.
K.әр сүзнең
Aboveгарыдагы нечкә диварлы корпусны эшкәртү ысулы нечкә диварлы корпус деформациясе яки зурлыгы һәм форма хаталары таләпләргә җавап бирә алмый.Тәҗрибә исбатлый, бу ысул эшкәртү эффективлыгы, уңайлы эшләве, озын һәм нечкә дивар өлешләрен эшкәртү өчен яраклы.Зурлыкны үзләштерү җиңел, һәм партия җитештерү тагын да практик.
Пост вакыты: 29-2022 сентябрь